Tal y como adelantábamos en la primera parte de este artículo sobre defectos internos en soldadura, vamos a continuar mostrando el aspecto macrográfico de los defectos que más habitualmente aparecen en las uniones soldadas utilizadas en la fabricación de construcciones soldadas.
Como decíamos, es importante conocer el aspecto que presentan estos defectos para identificarlos y relacionarlos con las causas que los producen. Ello nos permitirá actuar sobre dichas causas y evitar que vuelvan a aparecer.
Evidentemente los defectos que aparecen más habitualmente dependen del proceso de soldeo que se utilice. Por ejemplo, es evidente que la inclusión de escoria es típico del soldeo con electrodo revestido; mientras que no se puede aparecer en una pieza soldada con un proceso del tipo MIG-MAG.
En los cursos de soldadura que imparte SEAS, Estudios Superiores Abiertos, se describen las características de dichos procesos de soldeo, así como la defectología típica, relacionándola con las causas posibles. Este conocimiento también es necesario para la homologación como soldadores de los alumnos que realizan dicho curso. Si la unión soldada por estos alumnos durante la prueba no muestra defectos, queda superada la prueba de homologación, entregándose el correspondiente certificado de cualificación como soldador.
Por lo tanto, veamos a continuación la última serie de defectos más habituales en las uniones soldadas:
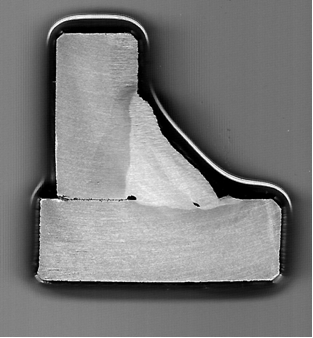
Macrografía de unión en ángulo de chapa gruesa (10mm), con falta de fusión entre pasadas y rechupe de raíz.
El rechupe en la raíz mostrado en la imagen anterior no es demasiado importante, dado que presenta una transición suave. No obstante, debe diferenciarse claramente de la falta de penetración, que lo haría inadmisible. Por el contrario, la falta de fusión entre pasadas, aun siendo de menor tamaño, es de mucha mayor importancia, puesto que es inadmisible, tenga el tamaño que tenga. A nivel resistente, se asemeja a una grieta que hará fallar la construcción soldada durante su uso.
La macrografía anterior, además de una preocupante falta de penetración, presenta también ángulo de acuerdo incorrecto y exceso de convexidad. En este caso, existe fusión, pero no hay penetración en la chapa inferior. En general, se considera un defecto grave que debe ser subsanado. La causa suele ser un ángulo incorrecto del electrodo, si partimos de la premisa de que la intensidad de soldeo empleada era la adecuada.
De nuevo, en la imagen anterior, la falta de fusión entre pasadas haría que esta soldadura fuese rechazada y debería ser reparada. Sin embargo, el poro aislado no tendría excesiva importancia. Puede observarse la clara diferencia existente entre el poro, de bordes circulares, y la falta de fusión, de bordes rectos, siguiendo las líneas de fusión de los sucesivos cordones depositados. La causa de un poro es la inclusión de gases, normalmente aire, formando una cavidad esférica, como si de un globo se tratara.
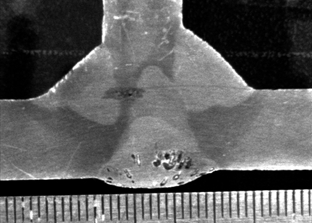
Unión especial de dos chapas a tope, unidas en ángulo con otra chapa, mostrando porosidad vermicular
Puede observarse en la macrografía anterior una alta concentración de poros vermiculares, en este caso en particular, causados por el hidrógeno de la humedad relativa del aire atrapado en la soldadura debido a una deficiente actuación del gas de protección de soldeo (proceso MAG).
Para finalizar, en la fotografía anterior puede verse un defecto extremadamente grave. La falta de penetración ha materializado una grieta que se propagará durante el uso de la construcción soldada hasta provocar su rotura total. En este caso, parece evidente que la causa es una deficiente preparación de bordes para la intensidad de soldeo empleada.
Tras lo anterior puede verse que un aspecto exterior impecable en una soldadura no es garantía de una soldadura de calidad, por lo que inevitablemente deben realizarse controles adicionales que complementen la inspección visual o el autocontrol del soldador.
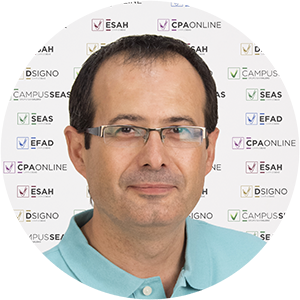
Graduado en Ingeniería Mecánica y Máster Universitario en Gestión y Diseño de Proyectos e Instalaciones Industriales. Ingeniero Europeo de Soldadura, Inspector de Construcciones Soldadas y Proyectista Instalador de Energía Solar. Profesor de las áreas de Energías Renovables, Soldadura y Diseño Mecánico en SEAS, Estudios Superiores Abiertos, centro de formación online del Grupo San Valero.