Los gemelos digitales (Digital Twins) son una de las tecnologías disruptivas transversales clave de la industria 4.0. Aunque no es un término ´trending topic´, los digital twins están llamados a transformar la forma en que entendemos las fábricas. Se trata de una de las tecnologías nativas de la industria 4.0 cuya principal virtud es aprovechar todo lo que nos aportan las otras tecnologías.
Pero hablar de gemelos digitales, a día de hoy, no es hablar de una solución cerrada y lista para usar. Es hablar de un proyecto de ingeniería y de desarrollo que crece día a día aprendiendo de sus errores.
Fundamento
En pocas palabras, un “Gemelo Digital” es un modelo virtual de un proceso, producto o servicio a través de la información obtenida fundamentalmente de sensores. Así que se trata de una especie de “avatares digitales” de los dispositivos y procesos que integran un entorno laboral, y que funcionan en conexión con el operativo real, que estos gemelos replican a través de Sistemas Ciberfísicos (CPS). En consecuencia, tenemos un sistema que aprende automáticamente cómo funciona un sistema real, con autómatas, robots, personas, vehículos, objetos, productos, etc. Esos sistemas están interconectados a través del ´Internet de las Cosas´ (IoT), generando un flujo de información muy grande que se recopila, sirviendo para aprender cómo se comporta el sistema monitorizado. Esta unión del mundo físico con el virtual permite el análisis inteligente de datos y la monitorización de sistemas para:
- Prevención de los problemas antes de que se produzcan.
- Prevención de los tiempos de inactividad.
- Desarrollo de nuevas oportunidades de negocio.
- Planificación futura mediante simulaciones.
- Customización del producto según los requerimientos del cliente.
Para poder entender cómo se genera un “Gemelo Digital”, hay que incidir en la importancia de la información proveniente del mundo físico. O sea, que si no disponemos de datos reales, no hay forma de implementar el ´digital twin´.
Una vez se obtiene el análisis del proceso, se puede generar de manera virtual el proceso, producto o servicio, y dotarlo de todos aquellos cambios, antes de ponerlo en fabricación. Si virtualmente se consiguen satisfacer los requisitos de un proyecto, entonces se pasa a la producción física.
El gemelo digital comienza con una copia digital de los elementos físicos de la planta (los sensores recopilan datos sobre el estado del proceso, producto o servicio en tiempo real). Los componentes están conectados a un sistema basado en ´La Nube´ que recibe y procesa la información obtenida. Un software específico compara todo lo obtenido, junto con otros parámetros contextuales.
Lo primero que nos permite esta forma de trabajar, es poder reproducir el estado de la planta en cualquier momento (permite enfocarnos mucho más en la causa raíz de los problemas). La segunda cuestión que nos permite esta forma de trabajar es la de predecir situaciones. Y finalmente, la tercera cuestión, la más pretendida, es al mismo tiempo la más difícil, lejana y complicada. Se trata de la capacidad de simulación, el objetivo último del gemelo digital. La tecnología del ´digital twin´ permite también virtualizar desde un producto hasta un proceso concreto, y esto constituye una herramienta muy potente y extremadamente versátil. De este modo, los gemelos digitales vigilan el ciclo de vida de un proceso replicando su funcionamiento en un modelo virtual que sirve como base para la experimentación.
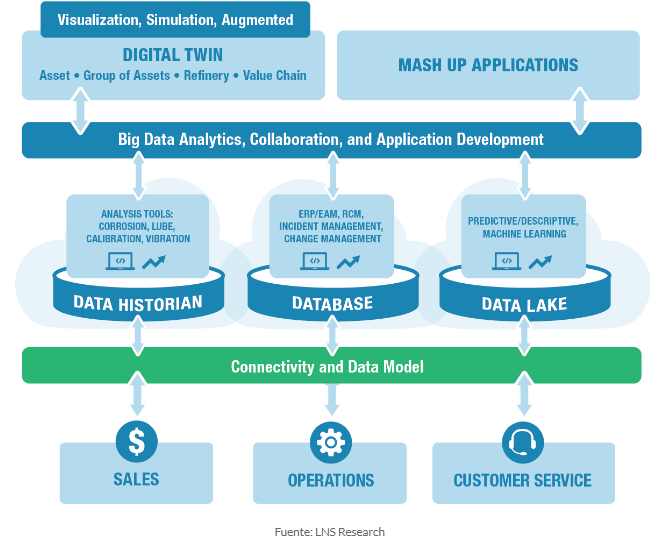
¿Qué conseguimos?
Este tipo de tecnología digital hace que empresas de todos los tamaños puedan cubrir sus demandas y conseguir reducir el time-to-market casi en un 50%, mejorar la flexibilidad e incrementar la productividad hasta un 20%, lo que determina la competitividad de las compañías. Algunas fuentes han estimado que, gracias al análisis y simulación virtual, las empresas podrían llegar a ahorrar un 70% de energía, cuestión que repercutiría en una importante reducción de costes tanto para el productor como para el consumidor final.
En consecuencia, conseguimos un entorno protegido y seguro para la experimentación, pudiendo detectar problemas antes de que ocurran, planificar tareas de mantenimiento evitando paradas inesperadas, construir nuevos escenarios de funcionamiento más eficientes (OEE), desarrollar nuevas oportunidades de negocio y nuevos planes de fabricación, o incluso realizar previsiones a futuro.
De hecho, el Gemelo Digital permite la producción de piezas personalizadas y adaptadas a las demandas y requerimientos específicos de los clientes. Evitando, con ello, la fabricación en masa de productos genéricos. Lo mismo ocurre con el servicio de mantenimiento. La simulación virtual de entornos físicos ayuda a que el trabajador pueda consultar y actuar con libertad de movimientos, al no tener que sostener ningún dispositivo.
Además, desde el punto de vista medioambiental, contar con procesos mucho más eficientes se traduce en una reducción considerable de las emisiones contaminantes.
Por otro lado, el análisis de los datos y la simulación posterior permite crear un comportamiento predictivo, cuestión esta muy demandada por cualquier sector de actividad humana.
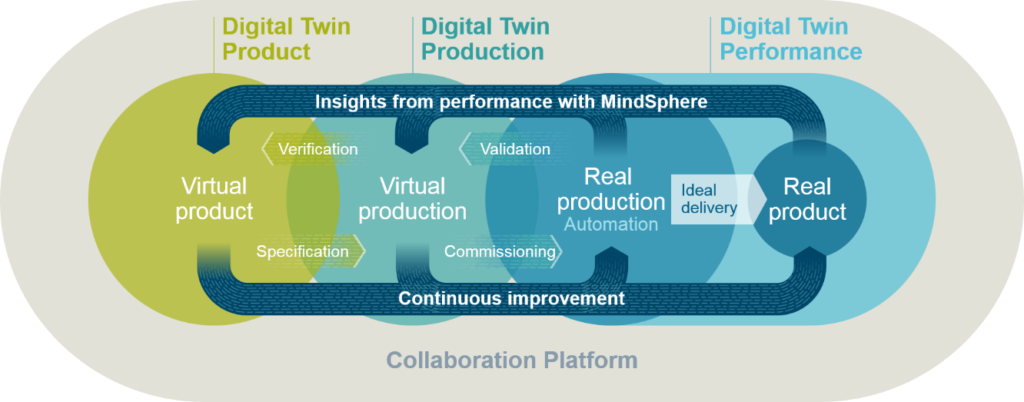
Límites
Sin embargo, el Gemelo Digital es todavía un concepto en pleno desarrollo que presenta diversas barreras tecnológicas para su incorporación al tejido industrial. Por un lado, existe una dificultad técnica para monitorizar masivamente y digitalizar procesos en la industria, con gran variedad de equipos, sistemas aislados, buses de campo, protocolos propietarios, así como una estricta arquitectura de integración y automatización industrial.
Por otro lado, los sistemas utilizados actualmente en la industria son incapaces de almacenar y tratar los volúmenes de datos necesarios para la completa creación y evolución de los ´Gemelos Digitales´, que realmente representen el comportamiento de los elementos físicos, y no sólo sus características y su estado.
Esto está unido a la complejidad tecnológica que requiere el ir más allá de las representaciones digitales y avanzar hacia escenarios de manejo de múltiples copias digitales simultáneas, con mayor capacidad de evaluar escenarios alternativos.
La abrumadora cantidad de datos que generan los sistemas de almacenamiento y tratamiento de la información proveniente del entorno 4.0, dificultan el seguimiento del trabajo, que no siempre puede atender a cantidades tan enormes de datos. Así que convertir la industria convencional en un sistema de ´data driven´, es un asunto nada fácil. De hecho, se estima que existen cuatro grandes barreras:
- La dificultad de digitalizar los sistemas en planta. Tal como están montadas, la mayoría de las plantas no es fácil sensorizar todo, ni implantar redes de IoT.
- La segunda barrera es gestionar en tiempo real el Big data, sobre todo con un nivel razonable de inversión.
- La natural resistencia al cambio. Digital twin implica apostar por una transformación muy importante en el medio-largo plazo.
- La necesidad de formación en las tecnologías propias de la industria4.0.
Conclusiones
Algunas de las empresas punteras en el campo de la automatización y las tecnologías emergentes han apostado por la utilización de los últimos avances en tecnologías del Internet de las Cosas Industrial (IoT), y en técnicas de Machine Learning basadas en el Big Data (uno de los grandes aliados del ´Digital Twin´). Por ello, las tecnologías Big Data pueden complementarse con los ‘digital twinning’ para crear escenarios de producción alternativos.
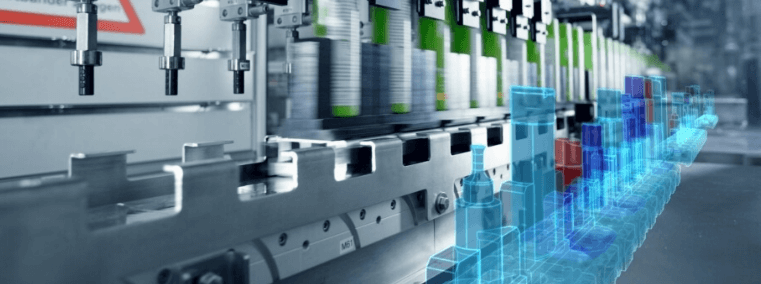
Al disponer de un producto conectado por vía inteligente a su representación virtual, será posible alcanzar objetivos más ambiciosos.
El objetivo último, todavía lejos de hacerse realidad, es contar con una gran factoría virtual que nos permita simular multitud de escenarios. Es decir, probar cambios en la producción, en los productos o en cualquier punto de la cadena sin afectar a la operación física real.
La cuarta revolución industrial implica mucho más que la dimensión tecnológica; tiene que ver con nuevos modelos de negocio, la gestión de riesgos o la eficiencia operativa. Se trata de revolucionar la industria con la tecnología y la digitalización como potente revulsivo. Y quizá los ´gemelos digitales´ engloban mejor que ningún otro nuevo sistema tecnológico, el gran paradigma de cambio que supone la industria 4.0.
Está claro que en el corto plazo, el ahorro inmediato no se consigue (aunque por ejemplo, un ´gemelo digital´ permite que varios equipos trabajen simultáneamente sobre él, reduciendo el tiempo necesario para poner en marcha una máquina o una línea de automatización en hasta un 30%.). Pero, en un plazo de cinco o diez años, quien no haya dado el paso, quizá no sea capaz de competir.
La mayor parte de los fabricantes que apuestan por la 4.0 ven en el retorno de la inversión, el beneficio más deseable de los ´gemelos digitales´. De esta forma, los proveedores serán capaces de enviar a los fabricantes el doble digital del producto que necesitan para probar el ensamblaje de sus componentes en una fábrica virtual, detectando los problemas de forma preventiva.
Si estás interesado en todo lo que tenga que ver con la era digital orientada a la industria, SEAS imparte en modalidad online el Máster en Industria 4.0 para que puedas especializarte.
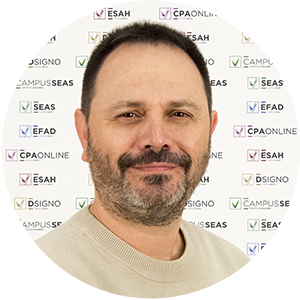
Manufacturing and Management Engineer y profesor del área de automatización industrial y también del área de mantenimiento y producción en SEAS, Estudios Superiores Abiertos, centro de formación online del Grupo San Valero. Puedes visitar su perfil en LinkedIn.