El objetivo principal de la automatización industrial consiste en gobernar la actividad y la evolución de los procesos sin intervención continua del operador humano.
En procesos de fabricación rígidos, de poca variación en el tiempo, o de carácter autónomo, sin interdependencia con otros tratamientos anteriores o posteriores de los productos, este objetivo se cumple programando sobre los controles locales de la planta las secuencias de control deseadas y cerrando los lazos de regulación necesarios para mantener los valores de variables en los rangos fijados por las consignas.
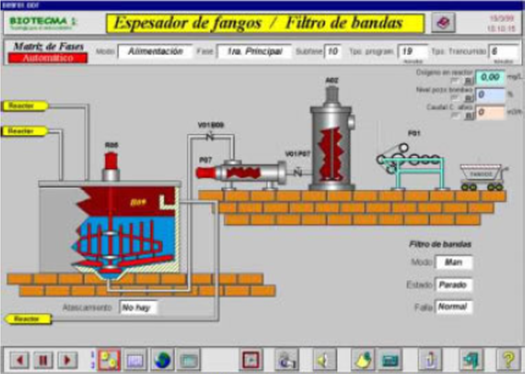
Sistema de supervisión de una planta de depuración de aguas
Desgraciadamente, la mayor parte de procesos industriales no cumplen aquellas condiciones, sino más bien las contrarias: han de ser flexibles, para adaptar la fabriación a la demanda de forma continua, y están firmemente interrelacionados entre sí, por exigencias de factores no sólo especificados de la producción, como la coordinación de las acciones o la continuidad del suministro en fabricación serie, sino también por otros hasta hace poco ajenos a la producción, como la minimización de costes de “stocks”, la calidad integral del producto y el impacto sobre el medio ambiente.
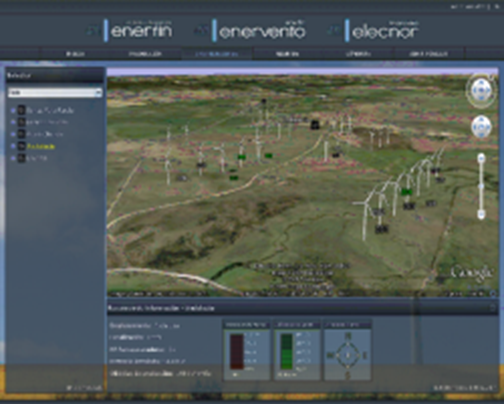
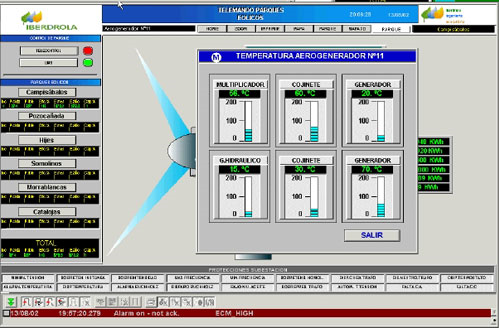
Aplicación de sistemas SCADA en parques eólicos
Estas necesidades obligan a disponer de sistemas automatizados de control de procesos industriales con un alto grado de complejidad y autonomía de funcionamiento, y funciones adicionales a las básicas de ejecución de tareas y monitorización de procesos. Aspectos como la toma (automatizada) de decisiones, la gestión de los menús de producción, la generación de históricos, gestión de alarmas, etc., así como los referentes al control de calidad y mantenimiento, quedan cubiertos en los niveles de control de producción y supervisión de planta del modelo jerárquico de automatización.
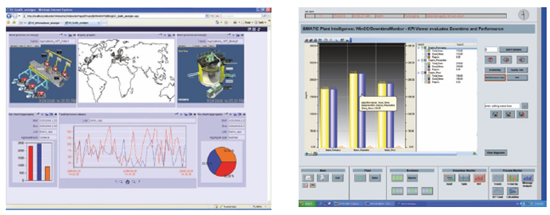
Generación de históricos y tendencias en un sistema de supervisión.
Para una buen control y supervisión de planta, es necesario un hardware y un software adicional que se adapten al sistema de producción. En el caso del software, utilizaremos unos paquetes integrados denominados “SCADAS” (Supervisory Control and Data Acquisition).
Los sistemas “SCADAS” permiten:
– La posibilidad de crear paneles de alarma, que exigen la presencia del operador para reconocer una parada o situación de alarma, con registro de incidencias.
– Generar históricos de señal de planta, que pueden ser volcados para su proceso sobre una hoja de cálculo.
– Crear informes (reports), avisos y documentación en general.
– Ejecutar programas, que modifican la ley de control, o incluso el programa total sobre el autómata, bajo ciertas condiciones.
– La posibilidad de programar numéricamente, que permite realizar cálculos aritméticos de elevada resolución sobre la CPU del ordenador, y no sobre la del autómata, menos especializado.
Con todas estas posibilidades, los sistemas SCADA, pueden desarrollar aplicaciones basadas en el PC, con captura de datos, análisis de señales, presentaciones en pantalla, envío de resultados, control de actuadores, etc.
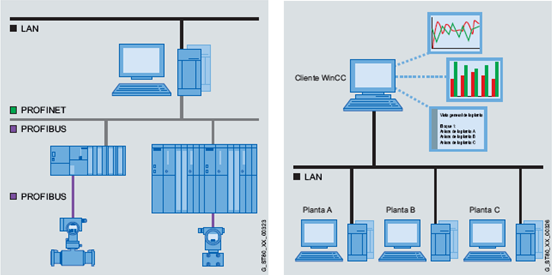
Arquitectura completa para un sistema de control y supervisión de planta “Scada”.

SEAS es el centro de formación online del Grupo San Valero, especializado en el ámbito técnico, industrial y de empresa. Visita www.seas.es para consultar nuestra oferta formativa de cursos y másteres. Formación profesional para el empleo de calidad y accesible para todos.